Copper Granulator User Guide
BSGH Granulator copper granulator can realize fully automatic mechanical separation and achieve the purpose of comprehensive utilization, with high economic benefits and no dust or secondary pollution. In addition, our copper granulator has an integral modular structure with stable performance, and it is easy to install, debug and transport.
knowledge about copper granulators
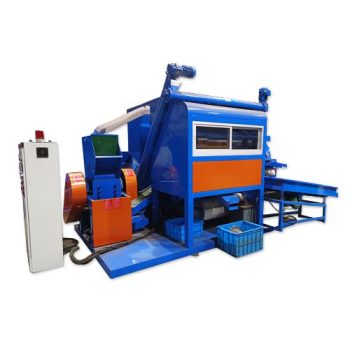
Copper granulators is a kind of recycling equipment designed for crushing and separating scrap copper from waste wires and cables, mainly consists of main crusher, airflow separator system(s), vibrating table, etc. Its working principle is to separate copper and plastic under the dual action of airflow separation and vibration.
We also have large copper granulators, medium copper granulators, and small copper granulators to choose from, and we can also customize single-phase electricity to suit different customers. Whether you are a small recycling station or a large-scale production enterprise, our products can provide efficient and reliable solutions.
Main Structure
- Shred your cables into copper and plastic particles, ready for the next step of separation
- Airflow separator system uses the weight difference between copper and plastic to separate the materials for the first time through wind power and vibration of the shaking table.
- At the copper outlet and plastic outlet, the vibrating table will separate materials for the second time, helping you obtain purer copper and plastic.
Table of Contents
how to install copper granulators?
This is very important when you begin to install machine, this is the basis of good separation effect and ensures you can use granulators well.
Installation requests
During installation, the copper granulator should be placed on a flat and solid ground stably and horizontally.
- If you buy a large copper granulator, you can ask our technicians to install it for you (you need to bear all the board and lodging expenses, round-trip air tickets and the technicians’ wages).
- If you buy a small copper granulator, you can install it yourself, it is very simple.
Stability means that there is no shaking or swinging in the whole machine during production. If there is shaking, use iron sheets to fill the gap between the machine chassis and the ground until the whole machine is no shaking. Level means that the material discharged from the copper outlet and plastic outlet is uniform. If materials discharging is uneven on both outlets, the outlet with more materials should be raised.
Connect to the power
Copper granulators generally use three-phase three-wire power supply.
- Firstly, connect the power supply and check if the voltmeter is the correct voltage.
- Secondly, the equipment should be grounded before use. Grounding requires inserting an iron bar into the ground, and then connecting the iron bar to the rack grounding bolt with a suitable copper wire.
- Finally, after the power cord is connected, check whether the spindle rotation direction is consistent with the arrow direction on the protective cover.
- If they are consistent, you can use the machine normally. If not, just swap any two live wires.
preare to running phase
- Preparation
- Before starting the machine, check whether there is enough grease ateach lubrication point, whether the bolts are tight, etc.
- Check whether there are any problems with the various parts of the machine, open the upper cover of the crusher, and turn the crusher shaft by hand to ensure smooth rotation without scratching the bottom sieve mesh.
- Start the machine:
- After turning on the power, turn on and off the power switches of each component one by one to see if the power connection is normal.
- Before starting the machine, clean the residues on the crusher and other parts to avoid increased load during startup.
- Operation instructions
- Turn on the equipment in order from the feeding part to the discharging end, including crusher, conveyor belt, airflow separator, etc.When starting the machine, please note: Turn on the No. 1 crusher start button, wait for 8 seconds, and then turn on the other buttons in sequence. Feeding should be even and continuous.
- After starting, the equipment should be idle for 5-10 minutes, pay attention to the operation of each component, and then load the material after all components operate without abnormality.
- Before turning off the machine, you must first stop feeding and wait for the material in the machine to be drained to avoid jamming when you turn it on again.
NOTE: If the cable contains iron, you can install a magnetic separator to remove iron from the recycled copper. If there is a large number of capillary wires, you can install an electrostatic separator. The electrostatic separator is installed at the plastic outlet to sort the material again, separating the copper that the air separator cannot select, ensuring the maximum recovery of copper in the cable and improving the recovery rate.
Common faults and solutions
1.Can't start normally
Reason
It may be that the wrong feeding and starting sequence causes the crushing chamber to be clogged, or the power supply may be faulty.
Solutions
Start first and then feed materials, ensure uniform feeding, and check whether the three-phase power supply is normal.
2. Clogging
Reason
The material is fed too quickly, air flow separator is not adjusted properly, or air duct is blocked.
Solutions
Control the material feeding speed, adjust the frequency of airflow separator, and clear the material blocking the air duct.
3. Poor separation
Reason 1
The copper granulator is not placed stably. Because the gravity separator of the copper granulator relies on vibration to separate copper and plastic. If the machine is also shaking, the two vibrations will offset each other, resulting in unclean separation.
Solution 1
The machine should be placed on a level ground to ensure that the copper granulator does not swing during the production process. If the shaking is caused by a gap between the machine chassis and the ground, you can insert iron sheets into it until the whole machine is no shaking.
NOTE: It should be noted here that you cannot use soft materials to pad the gap, nor can you raise all machine frame to leave the middle of the machine suspended in the air. Most of the machines should be in contact with the ground.
Reason 2
The airflow separator regulator is faulty or incorrectly set.
- The faster the shaking speed of the airflow separator, the more the plastic moves toward the copper outlet;
- The slower the shaking speed, the more the copper moves toward the plastic outlet.
- The smaller the air blowing volume, the further the plastic moves towards the copper outlet;
- The larger the air blowing volume, the further the copper moves towards the plastic outlet.
Solution 2
Check the working status of the airflow frenquencyThe shaking table speed should be based on when no plastic discharges from the copper outlet. If there is plastic discharging from the copper outlet, you can slowly increase the wind power until no plastic or a small amount of plastic discharges from copper outlet.
Note: There is a pressure plate at the copper outlet of the shaking table, which is adjustable in height. The lower the pressing plate is, the less likely it is for copper to discharge. Generally, the pressing plate is about 3cm away from the sieve surface.
Reason 3
The blade of the main crusher is not sharp enough or the gap between the moving blade and the fixed blade is too large. If the blade is worn or the gap is too large, it will affect the cable crushing effect, leading to poor airflow sorting effect.
Solution 3
- Check blade usage. Check the use of the blade regularly. If you find the blade is worn, sharpen it with a sharpener in time. You can continue to use it after it is sharpened, but be careful not to sharpen the blade manually.
- Adjust the gap between the moving blade and the fixed blade. The blade will become narrower after repeated sharpening. When the gap between the moving blade and the fixed blade cannot meet the crushing requirements, the old blade needs to be replaced.
Note: The moving blade edge should be 2mm-5mm away from the center bottom of the sieve mesh. On the premise that the moving blade and the fixed blade do not get stuck, the smaller distance between the moving blade and the fixed blade, the better (generally the gap is 0).
Reason 4
Sieve mesh is used not properly or blocked.
- If the mesh aperture is too small, metal particles can easily get stuck on the sieve mesh, causing the copper granulator to be clogged;
- if the mesh aperture is too large, metal and plastic particles can easily be sieved out together, which will affect the separation effect;
- If the mesh apertures are clogged, it will also lead to unclean separation, and may even cause the machine to not work properly.
Solution 4
Firstly,you need to choose a suitable sieve mesh. When processing wires of different materials and specifications, the copper granulator requires different sieve mesh to achieve the best separation effect. Therefore, the thinner the copper wire, the denser the mesh should be. Secondly, during production, the wind is sucked in through the air inlet filter, blown to the air separation sieve by the air blower, and then sucked away by the suction fan through the separation mesh and blown to the dust collector This continuous wind operation must be unobstructed, and any blockage will affect the separation effect. Therefore, the air inlet filter and separation mesh need to be cleaned in time.
- To see if the sieve mesh is clogged, you need to remove the sieve mesh and check whether there are little black dots on the mesh under light. If there are too many little black dots, it proves that the sieve mesh is clogged.
- When cleaning the screen mesh, if it cannot be blown off with a high-pressure air gun, you can brush it with gasoline and then blow it with a high-pressure air gun.
- Finally, an vent should be left on the dust collector bag, and the dust collector bag should be cleaned in time to prevent clogging.
help you quickly operate machine
-
If no copper is discharged from the copper outlet of the air separator table, increase the shaking table speed and reduce air blowing volume.
-
If a large amount of plastic discharges from the copper outlet of the shaking table, slow down the shaking table speed and increase the air blowing volume.
-
If no plastic discharges from the plastic outlet of shaking table, slow down the shaking table and increase the air blowing volume.
-
If a large amount of copper discharges from the plastic outlet of the shaking table, increase the shaking table and reduce air blowing volume.
-
Notice - Very important
The airflow separation and vibration work together simultaneously, means when you operate machine, you can't adjust one only, you need to adjust one and the other one is cooperate to this one to achieve the best separation effect. If you not know how to adjust , pls contact our staff.
*If you buy our machine, We have a variety of machine parameter lists for different wire configurations. you can request them from our sales staffs.
Maintenance
1. Add Resistant Grease
- Crusher, separator, electrostatic separator and crusher main bearings should be filled with high-pressure and high-temperature resistant grease every three months.
- The main bearing of separator and the eccentric bearings on both sides should be filled with high-temperature resistant grease every four months.
- The main bearing of the electrostatic separator should be filled with high-temperature grease once a year.
- In addition, main crusher’s rotating shaft bearings need to be greased frequently (generally 300°-500° high-temperature grease should be added three to four times a month).
2. How to remove crusher blades?
After copper granulator’s blades has been used for a period of time, the crushing effect will deteriorate. You can remove the blade, sharpen it with a sharpener, and then reinstall it for continued use.
There is no order for removing the blade, just loosen the screw and take off the blade. The specific method is as follows:
- First loosen the box connecting screws, push the upper box backwards, use an electric wrench to remove the screws fixing the blade, and then you can remove the blade.
how to install crusher blades?
Install the inner fixed blade first, put the fixed blade edge upwards, and place the tool bar with the milling groove facing downwards on the box boards on both sides. Put the two ends of tool bar close to the inner box board, with the fixed blade edge close to the tool bar, and tighten the screws.
Then install the moving blade, taking the inner fixed blade edge as the reference, all the moving blade edges and the fixed blade edges have zero gap, and do not touch the blade edges after fixing.
③Finally, install the outer fixed blade with the blade facing downwards. Using any moving blade as a reference, there should be zero gap between the fixed blade and the moving blade, and they should not touch each other during rotation.
After all blades are installed, tighten all blade pressing screws, then pull the spindle by hand to rotate and check whether the blades are properly installed. At last, clean the foreign objects around the box, close the upper box and tighten the upper box connecting screws.
3. Replace sieve mesh
- Remove the left and right connections at the bottom, loosen the screws, then you can lay down the chassis and pull out the sieve mesh.
- After the sieve mesh is installed and the lower box is closed, be sure to open the upper box to check whether the front and rear of the sieve mesh are stuck under the fixed blade bottom plate.
You can click on the video link on the right to watch the specific process of replacing the screen.
4. Air blowing cleaning
After each use, clean the air filter around the air separator shaking table.
- When cleaning, it is best to use a vacuum cleaner to remove the dust on the filter surface so that the air intake is normal when used next time.
- After cleaning the filter, remove the sieve mesh on the shaking table and clean the sieve mesh with a high-pressure air gun.
- After removing it, turn on the vacuum fan first, and then turn the variable frequency fan to its maximum (50HZ).
- This will clean up all the dust in the air duct. After cleaning, just install them one by one.
You can click on the video link on the right to watch the specific process of cleaning the screen
5. Dust collector bag cleaning
When the dust collector bag is working, clean it every 2 hours or so.
- open the upper dust collector bag door and tap the dust collector bag gently with a small wooden stick to let the dust on the dust collector bag fall off, ensuring the normal operation of the dust collector bag.
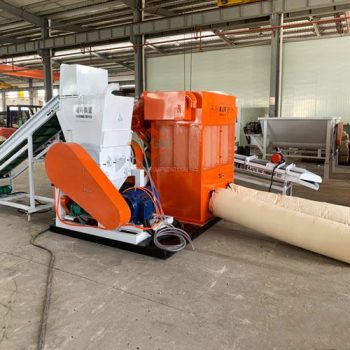
Our Services
Precautions
read operating instructions
Before using the copper granulator, you need to read the machine operating instructions carefully and operate it in accordance with the operating procedures.
processed separately
When the copper granulator is in production, the materials should be processed separately, and copper wire and aluminum wire should not be mixed together. In addition, try to avoid mixing thick and thin wires into the machine to avoid affecting the sorting effect.
avoid blockage and overload
Feed the material evenly to avoid blockage and overload. If vibration, noise, bearing overheating, etc. occur, stop the machine immediately for inspection.
Security Awareness
When operating the copper granulator, you need to pay attention to safety to avoid accidents.
Don't teardown
Operators are not allowed to dismantle the equipment without permission, and maintenance tools are not allowed to be placed inside the equipment.
Dry place installation
The copper granulator is best installed in a dry and well-ventilated place.
Lets Tell Us About Your granulator machine Needs
- Whatsapp/Viber: 008613772508206
- Email: coppergranulator@bsghrecycling.com
- Website: https://bsghgranulator.com/