For Scrap Cable Recycling Fields
Ⅰ. Introduction
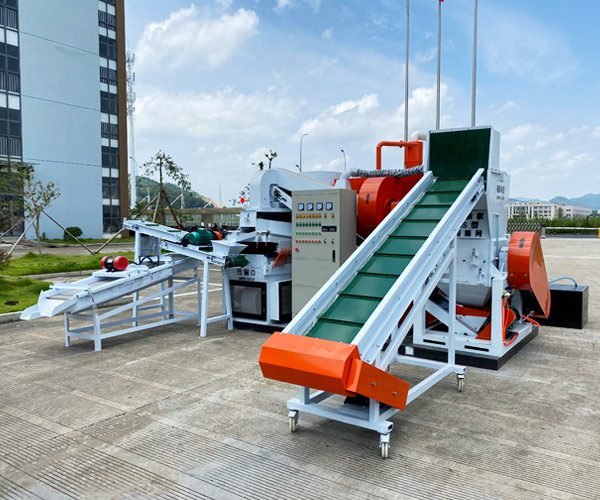
The dry copper granulator is a highly efficient and environmentally friendly equipment specially designed for processing scrap cables and wires. It separates the copper wire from the plastic insulation layer by physical methods, thereby realizing the recycling of copper and plastic. The emergence of dry copper granulator has completely changed traditional recycling methods. It not only helps to protect the environment and reduce resource waste, but also creates more economic benefits.
This article will introduce the working process of the dry copper granulator in detail to help you better understand the working principle and operation steps of the dry copper granulator machine.
Ⅱ. Dry Copper Granulator Machine Overview
Firstly, you need to know the structure, operation steps and working principle of the dry copper granulator.
⭐ Structure of Dry Copper Granulator
Our copper granulator machine is mainly composed of the following parts:
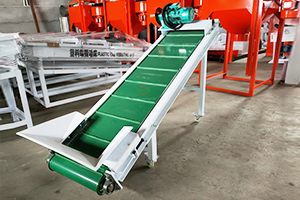
Conveyor Belt
Convey the scrap cables and wires, wire segments or plastic granules to the next processing step.
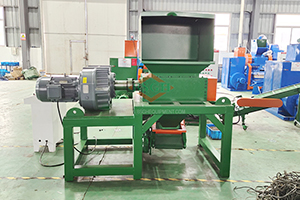
Pre-shredder
Process the scrap cables and wires into 5-10 cm segments for the first time.
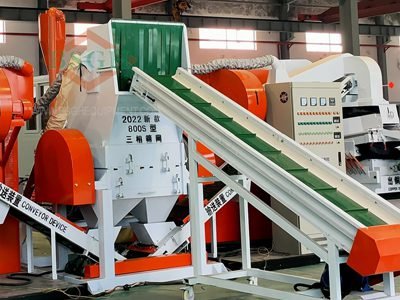
Main Crusher
Crush the small segments into a mixture of copper and plastic granules.
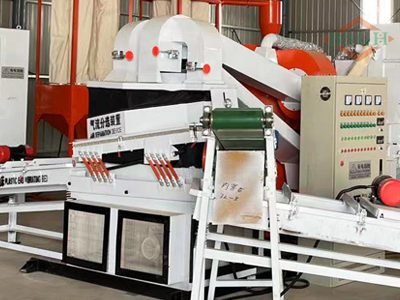
Air Separator
Under the action of vibration, the copper and plastic particles are sort through their different weight
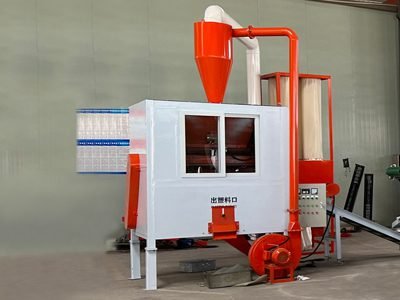
Electrostatic separator
Separate copper and plastic particles by taking advantage of the difference in conductivity between copper and plastic.
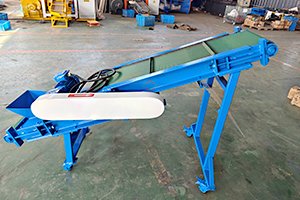
Magnetic Separator
Absorb the iron contained in copper granules during production process, and reduce the wear of the copper granulator machine blades.
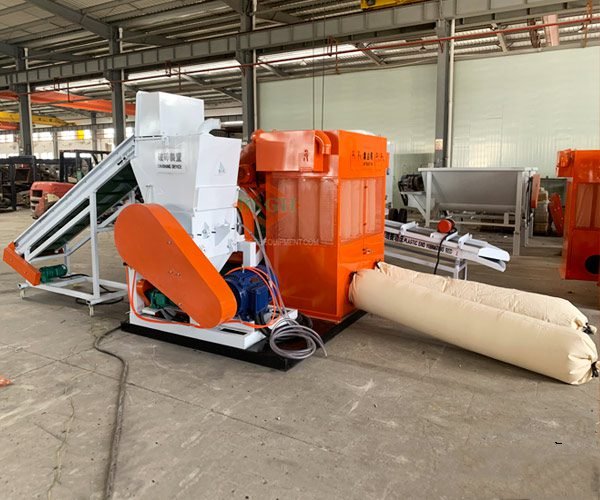
Dust Collection
Reduce dust pollution during the production process and ensure the cleanliness of the production environment.
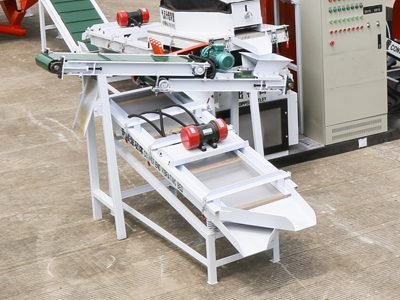
Small Vibrating Table
Copper and plastic can’t be completely separated by air separator, small vibrating table is connected after copper outlet and plastic outlet, allowing for a higher level of purity in the final product by vibrating.
⭐ The Working Principle of Dry Copper Granulator
The working principle of the dry copper granulator is based on physical crushing and separation technology. The crusher uses high-speed rotating blades to process the scrap wires and cables, and crush them into copper granules. Airflow separator is to effectively separate copper and plastic by utilizing the weight difference between copper and plastic in the air. Its principle is based on the airflow separator. Through the wind blowing upward from the bottom of the shaking table and the vibration of the shaking table, the copper granules move toward the copper outlet and the plastic particles move toward the plastic outlet, thereby achieving the screening of copper and plastic.
⭐ The Operating Steps of Dry Copper Granulator
- Pre-shredder processes scrap wires into 5-10 cm segments;
- Scrap wire segments are conveyed to the main crusher by conveyor belts;
- The main crusher processes wire segments into the mixture of copper-plastic granules;
- Convey belts convey mixture copper-plastic granules to air separator system for the first separation;
- The copper granules and plastic particles are respectively conveyed to a small vibrating table for the second separation;
- The copper outlet is configured with a magnetic separator to remove iron from copper granules. The plastic outlet is equipped with an electrostatic separator to separate the copper from the plastic again.
- Finally, you can get pure copper granules and plastic particles.
Ⅲ. Dry Copper Granulator Working Process
The whole working process of the dry copper granulator can be roughly divided into the following four stages:
⭐ Preparation
The preparation phase mainly includes scrap wires collection and sorting, safety inspection, and power supply check.
Scrap Wires Collection and Sorting: You need to collect scrap wires and cables to process firstly. These scrap cables may come from various sources, such as discarded electronic products, construction sites, etc. Then the collected scrap cables need to be initially sorted to ensure that the equipment can effectively separate scrap wires of different materials, for example, separate the copper and aluminum wires.
Safety Inspection: Before starting each time, the entire dry copper granulator line should be allowed to idle for 2 to 3 minutes to observe whether the equipment is operating normally. Only when there is no abnormality can the material be put into production. This is to ensure that the equipment is in good condition before formal operation to avoid production interruption due to equipment problems.
Power Supply Check: Turn on the power supply and thoroughly check whether there are any problems with the equipment, such as loose bolts, etc. After turning on the power supply, turn on and off the power switches of each device one by one to observe whether there are any problems with the motor direction.
⭐ Crushing
The crushing stage mainly includes pre-treatment and fine crushing.
Pre-shredder
The scrap wires are put into the shredder, and then the two sets of blades rotating in opposite directions are used to process the scrap wires into small segments of about 5-10 cm. This pre-treatment method can increase the output of the dry copper granulator and improve working efficiency.
Main crusher
After shredding, the next step is further crushing. The shredded scrap wires are conveyed to the main crusher via a conveyor belt, then the crusher processes small segments into the mixture of copper-plastic granules, ensuring that the crushed materials can reach the particle size required by the dry copper granulator separation system.
⭐ Separation
The separation stage of the dry copper granulator is a key part of the entire workflow. The separation system of machine mainly includes four types separator:
Airflow Separator
The airflow separator is configured behind the crusher. It mainly utilizes the different densities of copper and plastic, and then separates copper and other metals from plastic in scrap wires through wind power and amplitude movement on the sieve surface. The mixture of copper-plastic particles are conveyed to the airflow separator through a conveyor belt. The wind blowing upward from the bottom of the sharking table blows up the plastic particles. At the same time, under the action of the vibration of shaking table, the copper particles move toward the copper outlet, and the plastic particles move toward the plastic outlet, completing the first separation.
Vibrating Table
Two small vibrating tables are respectively installed at the copper outlet and the plastic outlet for the second separation. The vibrating table has two layers, the upper layer is a sieve mesh, which is used to screen copper granules and plastic particles of suitable size. Specifically, normal-sized copper and plastic particles fall through the mesh onto the vibrating table, while big copper and plastic particles are left on the sieve mesh, waiting to be separated again.
Magnetic Separator
Magnetic separator uses magnetic force to separate iron and copper. Through the action of the magnetic, iron will be adsorbed on the magnetic field, thereby obtaining pure copper granules. There are two magnetic separators: high strengthen magnetic separator and magnetic separator. The high strengthen magnetic separator is usually configured behind the pre-shredder, to absorb iron block. If the wires contain iron, which can be separated by the high strengthen magnetic separator after shredding, reducing the wear on the crusher blades. The magnetic separator is usually equipped on the copper outlet to remove iron chips mixing in the copper granules.
Electrostatic Separator
Electrostatic separator uses the electrostatic effect to separate different materials. This separation method is based on the difference in electrical conductivity between copper and plastic, and it is used to recover copper powder mixed in plastic particles, thereby increasing the recovery rate of copper.
⭐ Discharging
The main purpose of this stage is to collect and package the separated copper and plastic materials. The copper and plastic granules processed by the dry copper granulator machine can be reused to manufacture new electronic products or other industrial products, realizing the recycling of resources.
The following is the process flow chart of the dry copper granulator, which will help you understand the working process of the copper granulator machine more intuitively.
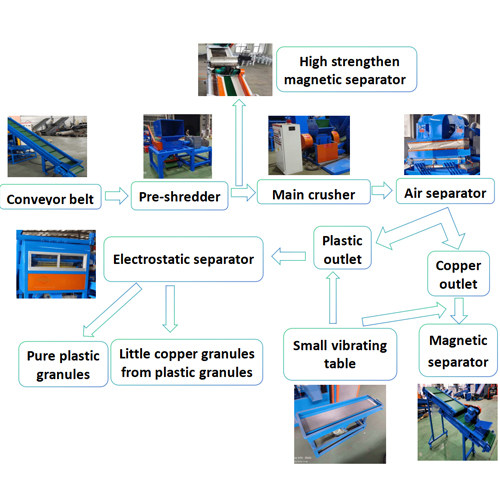
Note: The above dry copper granulator’s working process is only applicable to our company’s machine. If you need it, please contact us and we will provide you with professional services.
???? Jocy: 0086 13772508206
???? Email: coppergranulator@bsghrecycling.com
Ⅳ. The Advantages of Dry Copper Granulator
The main advantages of the dry copper granulator can be summarized as follows:
Efficient Processing
The dry copper granulator can directly process scrap wires without tedious sorting work, saving manpower and time costs. It has efficient working capabilities and can quickly process large amounts of scrap wires, significantly improving processing efficiency.
High Resource Recovery Rate
The dry copper granulator uses advanced processing technology to completely separate the copper and plastic in scrap wires and cables. This not only maximizes the recovery and reuse of copper resources in scrap wires, but also effectively reduces the pollution caused by waste plastics to the environment.
Significant Economic Benefits
The copper resources in scrap wires and cables have high economic value. The use of dry granulator machine can efficiently recycle copper resources in scrap wires, thereby obtaining more economic benefits. At the same time, the high processing efficiency and low labor cost of the dry copper granulator also increase its economic benefits.
Good Environmental Performance
The dry copper granulator is equipped with a dust collection, which can effectively reduce the pollution of dust and particulate matter generated during the processing. The dust collection can capture and absorb dust particles in the crushing process in time and process them, so that the air quality is effectively guaranteed and the handling process is more environmentally friendly.
Ⅴ. Conclusion
The dry copper granulator improves the processing efficiency of scrap wires and cables with its excellent performance. Through its sophisticated work process, the dry copper granulator ensures the efficient separation of copper and plastic, greatly improving the copper recovery rate, which can help you get more profits and make your recycling business more brilliant.
Through the above article, you can understand the working principle and workflow of the dry copper granulator machine, as well as its advantages in the recycling of scrap wires and cables. I hope this article will be helpful to you.