If your shredder blades are dulling quickly or chipping often, this problem will kills productivity and reduce profits which is a major trouble for recycling operations. The key to solving it? Choosing the right blade material is critical.
There’s no single “best” material for shredders; it depends heavily on what you’re shredding. High-performance options often include Tool Steels (like D2/SKD-11) for hardness and wear resistance, specific alloys (like 9CrSi) for cost-effective wearing in applications like cable granulation, shredders or tougher Alloy Steels for handling more rigid materials.
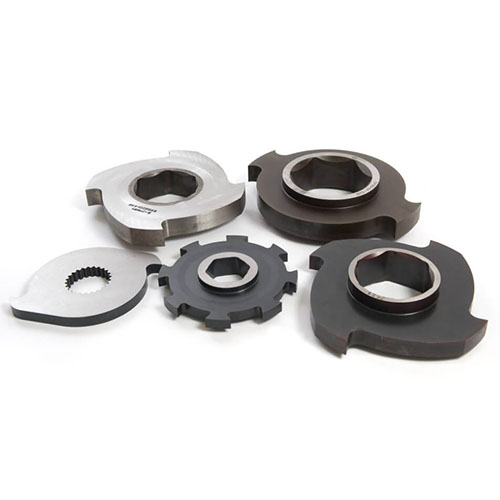
As manufacturers of recycling equipment like copper granulators here at BSGH, we understand that shredder blades are the heart of the machine. They do the tough work. Selecting the wrong material means frequent replacements, poor shredding quality, and higher operational costs. Let’s look into what makes a good blade and the common material choices available so you can make a wise decision.
What Are the Common Shredder Blade Materials Available?
Feeling lost in a sea of steel codes like D2, H13, 9CrSi, SKD-11? Choosing the wrong one based just on code or price can be a costly mistake. Let’s decode some common options.
Common choices include Tool Steels (D2/SKD-11 offer great wear/hardness), Alloy Steels (better toughness for impact), High-Speed Steel (excellent edge holding, often pricey), and specialized Cold Work Die Steels like 9CrSi (good wear/cost balance for applications like cable shredding).
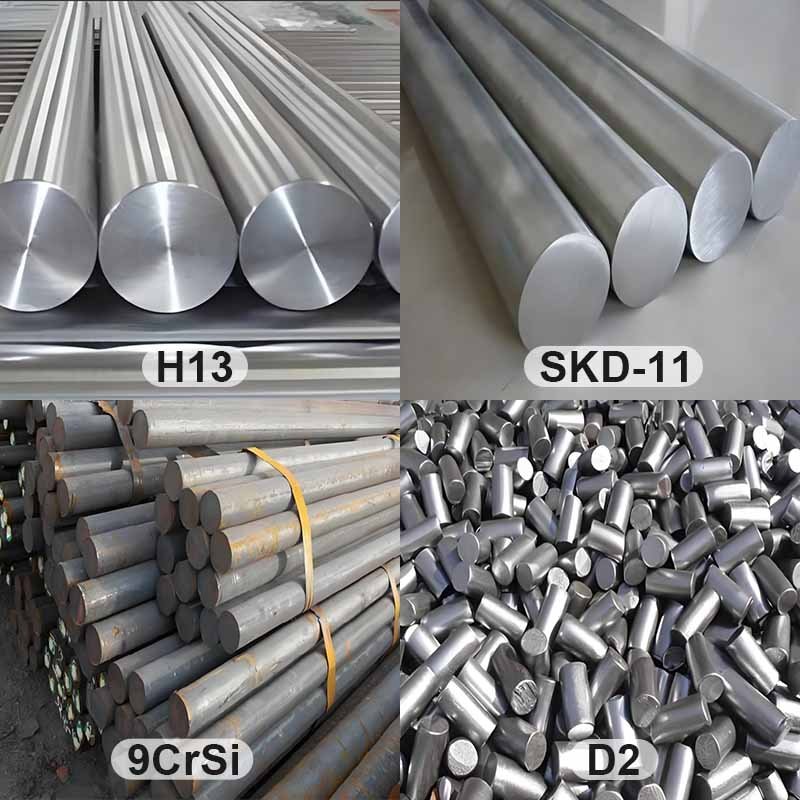
Understanding the basic categories and popular examples helps narrow down the choices. At BSGH, we select materials based on decades of experience and tailor them to the machine’s intended use, offering customization for specific client needs. Here are some common materials you’ll encounter:
1. Tool Steel (e.g., D2, H13):
- D2 (and its common equivalent, SKD-11): This is a very popular choice. It’s a high-carbon, high-chromium tool steel known for its excellent wear resistance and good hardness. It holds an edge well, making it great for shredding metals, plastics, and general scrap where abrasion is high. It’s a solid balance of performance and cost.
- SKD-11 is the Japanese Industrial Standards (JIS) equivalent, widely used in high-quality machines across Asia and globally.
- H13: This is a hot-work tool steel, meaning it retains strength at higher temperatures. It offers very good toughness and hardness, making it resistant to chipping from heat or impact. It might be chosen for applications with high friction; most of our shredder blades adopt H13.
2. Alloy Steel (e.g., variants of CrMo or NiCrMo steels):
These steels have specific elements added (like Chromium, Molybdenum, Nickel) to enhance properties, particularly toughness and resistance to shock loading. They might not hold an edge quite as long as D2 but are less likely to fracture under heavy impact, suitable for shredding mixed, bulky scrap where foreign objects might be present. Regular sharpening is often needed.
3. High-Speed Steel (HSS):
Originally developed for high-speed cutting tools, HSS variants offer superior hardness and wear resistance, especially at higher temperatures generated during cutting. They maintain a sharp edge for a very long time. However, they are typically more expensive and can be more brittle, making them less common for the rough-and-tumble world of primary scrap shredding, though sometimes used in granulators for fine cutting.
4. Cold Work Die Steel (e.g., 9CrSi):
This is a type of alloy tool steel often used where high wear resistance and decent toughness at room temperature are needed. We frequently use high-quality 9CrSi in the shredders integrated with our BSGH copper cable granulators. It offers a great balance of high wear resistance (handling the abrasion from wire insulation and copper) and cost-effectiveness, providing excellent performance life for this specific application without the higher cost of D2/SKD-11. Good heat treatment is vital for this material.
Material Category | Common Examples | Key Strength(s) | Potential Weakness(es) | Typical Use Case |
---|---|---|---|---|
Tool Steel | D2, SKD-11 | High Wear Resistance, Good Hardness | Moderate Toughness | General Metal, Plastic, Cable |
Tool Steel | H13 | Good Toughness, High Temp Strength | Moderate Wear Resistance | Impact-prone, Hot applications |
Alloy Steel | CrMo variants | High Toughness, Shock Resistance | Lower Wear Resistance | Mixed/Bulky Scrap, Heavy Impact |
High-Speed Steel | M-series, T-series | Superior Edge Retention, Hardness | Higher Cost, More Brittle | Precision cutting, Granulators |
Cold Work Die Steel | 9CrSi | Good Wear Resistance, Cost-Effective | Requires quality heat treatment | Cable Granulators, Specific Metals |
What Makes a Shredder Blade Perform Well and Last Longer?
Four key properties determine blade performance and lifespan: Hardness (resists deformation and keeps edge), Wear Resistance (fights abrasion from material), Toughness (resists chipping or breaking under impact), and sometimes Corrosion Resistance (fights rust).
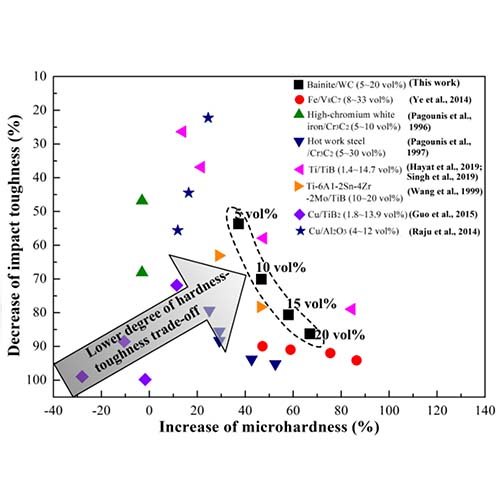
Choosing the right blade material isn’t just about picking a name from a list. It’s about understanding the demands of your specific shredding task and matching them to the inherent properties of the steel. Let’s break down these crucial factors:
- Hardness (Sharpness & Strength): This refers to the steel’s ability to resist scratching, indentation, and deformation. A harder blade holds its sharp edge longer, cutting cleanly and efficiently. However, extreme hardness can sometimes lead to brittleness. It’s measured using scales like Rockwell C (HRC).
- Wear Resistance: This is the blade’s ability to withstand abrasion as material rubs against it during shredding. High wear resistance means the blade lasts longer before needing sharpening or replacement, especially crucial when processing abrasive materials like dirty scrap or wire with gritty contaminants. Materials like D2 or 9CrSi excel here.
- Toughness: This is the blade’s ability to absorb energy and resist chipping or fracturing when subjected to sudden impacts or shocks. Shredding involves immense forces, especially with unevenly fed material or occasional hard contaminants (like a stray bolt). Tougher steels (often alloy steels) might sacrifice some hardness but are less likely to break catastrophically.
- Corrosion Resistance: While often less critical than the other factors in typical dry shredding, if you process wet materials or operate in humid environments, resistance to rust and corrosion becomes important to maintain blade integrity and performance. Some materials offer better inherent corrosion resistance than others.
There’s often a trade-off: extremely hard materials might be less tough and vice-versa. The ideal blade material finds the right balance for your specific application.
Property | What it Means | Why it Matters in Shredding | Desired Level Depends On… |
---|---|---|---|
Hardness | Resists deformation, keeps sharp edge | Cutting efficiency, edge retention | Material type, desired particle size |
Wear Resistance | Resists abrasion | Longer lifespan, less sharpening | Abrasiveness of material, volume |
Toughness | Resists chipping/breaking under impact | Prevents catastrophic failure, safety | Likelihood of impacts, contaminants |
Corrosion Resistance | Resists rust/chemical attack | Longevity in wet/humid conditions | Operating environment, material moisture |
How Do You Choose the Right Blade Material For Your Shredder?
Knowing the material options is helpful, but how do you pick the best one for your specific situation? Making the wrong choice means you’re either overspending or facing premature failure. Let’s focus on the decision process.
Key factors are: the material you shred (abrasiveness, hardness, uniformity), your expected throughput volume, acceptable maintenance frequency (sharpening/replacement), your budget constraints, and critically, ensuring proper heat treatment of the chosen steel.
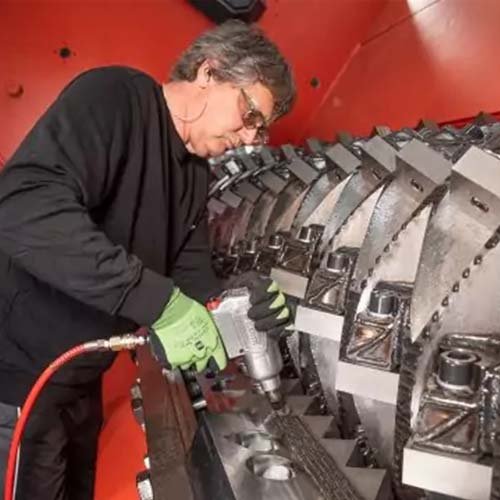
Selecting the optimal blade material is a balancing act. As a business owner, you need reliable performance without breaking the bank. Here’s what you, and we at BSGH when advising clients, need to consider:
- Material Being Shredded: This is paramount. Shredding abrasive materials like insulated copper wire puts high demands on wear resistance (favoring D2, SKD-11, 9CrSi). Shredding bulky scrap with potential contaminants requires high toughness (favoring Alloy Steels or H13). Soft plastics might allow for less demanding, cheaper steels.
- Production Volume: High-volume operations processing tons per hour need blades that last. Investing in higher wear resistance (D2, SKD-11) pays off by reducing downtime for blade changes, even if the initial cost is higher. Lower volume operations might manage with less wear-resistant but tougher or cheaper options.
- Maintenance Cycle: How often should you stop production for blade sharpening or replacement? If you need long intervals between maintenance, prioritize wear resistance and edge retention (D2, SKD-11, potentially HSS if budget allows). If frequent sharpening is feasible, tougher but less wear-resistant alloys might suffice.
- Budget: High-performance steels cost more initially but can offer lower cost-per-ton processed due to longer life and less downtime. You need to weigh the upfront investment against the total cost of ownership. Sometimes, a cost-effective option like 9CrSi (when properly heat-treated) offers the best value for specific tasks like cable granulation.
- Heat Treatment: This is crucial! The final properties of any steel blade depend heavily on the heat treatment process (hardening and tempering). Even the best steel type will perform poorly if not heat-treated correctly. Always ensure your supplier uses proper, controlled heat treatment methods tailored to the specific steel grade. At BSGH, this is a non-negotiable part of our quality control.
Consideration Factor | If Shredding Abrasive Wire… | If Shredding Bulky Scrap w/ Impacts… | If High Volume… | If Lower Budget… |
---|---|---|---|---|
Primary Need | Wear Resistance | Toughness | Wear Resistance, Durability | Cost-Effectiveness |
Likely Material Choice | D2, SKD-11, 9CrSi | Alloy Steel, H13 | D2, SKD-11 | Well-treated 9CrSi, Standard Alloys |
Key Trade-off | May sacrifice some toughness | May sacrifice some wear resistance | Higher upfront cost | Potentially shorter life/more maintenance |
By carefully considering these factors, you can select a blade material that provides the optimal blend of performance, durability, and cost-efficiency for your specific shredding needs.
Conclusion
Choosing the best shredder blade material isn’t simple, but understanding properties and options helps. Match the steel to your specific shredding job and operational needs for optimal performance, durability, and cost-effectiveness. BSGH offers expert advice and customizable blade options.