Ⅰ. What is electric motor?
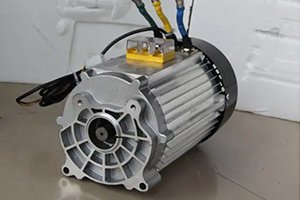
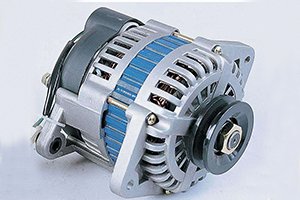
A motor is an electrical device that can convert electrical energy into mechanical energy and generate kinetic energy to drive other devices. Its working principle is to generate rotational torque through the interaction between the magnetic field and the winding current. Motors have many uses, from heavy industrial machines to small toys. They are widely used in home appliances, industrial production lines, transportation and other fields, such as air conditioners, washing machines, electric fans, power tools, electric vehicles, etc.
Ⅱ. How Many Type of Electric Motors?
Motors can be divided into DC motors, AC motors and pulse motors according to the type of power supply.
1. DC Motor
DC motors are only used in direct current conditions. They use permanent magnets or electromagnets, brushes, commutators and other components. The brushes and commutators continuously supply the DC power supplied by the power supply to the rotor coils, so that the rotor can continue to rotate in the same direction. Its speed can be easily controlled by simply changing the voltage, and its operating cost is very cheap. DC motors can be divided into brushed and brushless types according to their different structures and working principles.
- Brushed DC motor is a rotating motor with a brush device inside, which can convert DC power into mechanical energy or mechanical energy into DC power. It has the characteristics of fast starting and good speed regulation performance and is widely used in electric locomotives, internal combustion locomotives, electric bicycles, marine machinery, and other fields.
- Brushless DC motor replaces traditional contact commutator and brush using an electronic switching device. It has the advantages of high reliability and low mechanical noise, it is often used in medical equipment, household appliances, electric vehicles, and other fields.
Advantages Of DC Motor
1. Good torque characteristics:
- The relationship between the DC motor speed and torque is relatively simple and clear, and it is easy to achieve speed regulation and load balance.
2. Easy starting and reversing:
- DC motors have good starting and reversing capabilities and can accelerate from a stationary state to a set speed in a very short time. At the same time, reverse rotation is also very easy to achieve.
3. Easy to control:
- Since we can control the output torque and speed of the DC motor through current control, its operating state, including speed, torque, and other parameters can be precisely controlled.
4. High efficiency and energy saving:
- DC motors are high-efficiency motors with the characteristics of high efficiency, low power consumption, low noise, low vibration, etc., and can achieve high-quality and high-performance power output.
2. AC Motor
AC motors are another major type of motors. AC power is passed through the stator wingdings of the motor, and the surrounding magnetic field is designed to push the rotor at different positions to keep it running. They only require very low power when starting and can control acceleration, which means they can maintain constant speed and performance. AC motors can be divided into single-phase motors and three-phase motors.
- A single-phase motor is a small-power motor powered by a single-phase AC power supply (220V) with two-phase windings on its stator. Due to its convenient and economical features, it can be seen in almost all small-power household appliances.
- Three-phase motor is a type of electric motor powered by 380V three-phase AC, there are three-phase windings on its stator. Compared with single-phase motors, three-phase motors have better movement performance and can save various materials. They are widely used in industrial production lines, manufacturing, transportation, and other occasions that require high power output.
Advantages Of AC Motor
1. Simple Construction:
- AC motors are made up of a small number of parts, with a simple structure and low maintenance costs.
2. Reliable Operation:
- AC motors have the characteristics of long service life, high stability, and reliable operation, and are not easily affected by factors such as ambient temperature and humidity.
3. Wide speed adjustment range:
- The speed of the AC motor can be adjusted in a variety of ways with a wide adjustment range to adapt to different working conditions and needs.
3. Pulse Motor
A pulse motor is a motor that uses a pulse signal as a control signal. Its movement is controlled by a pulse signal sent by a controller to control the movement of the rotor. The controller controls the direction and speed of the motor’s rotation by adjusting the frequency and size of the pulse signal.
Advantages Of Pulse Motor
1. Accuracy:
- Pulse motors have high positioning accuracy. They can control the step angle according to certain rules to achieve high-precision positioning.
2. Control Method:
- Pulse motors are easy to maintain and the control system is relatively simple. Generally, open-loop control is sufficient.
3. Long Service Life:
- Many parts of pulse motors are frictionless. Bearings are the only parts that wear out and have a longer service life.
4. Applicable Scenarios:
- Pulse motors have great advantages for applications that require high-precision positioning, such as electronic equipment manufacturing, semiconductor processing, etc.
Compared with DC motors, AC motors lack converters, so their structure is simple, easy to manufacture, relatively strong, and suitable for large machines with high speed, high voltage, and high current requirements. The scrap metal recycling machines in the recycling industry use AC motors, which are used in conjunction with three-phase or two-phase power supplies to ensure reduced wear when processing scrap metals such as iron and copper, making them more durable than other types of motors.
Ⅲ. The Structure of Scrap Metal Recycling Machine Motor
Common scrap metal recycling machine motor structures on the market are very similar, mainly composed of a stator, a rotor, and a motor casing.
1. Motor Stator
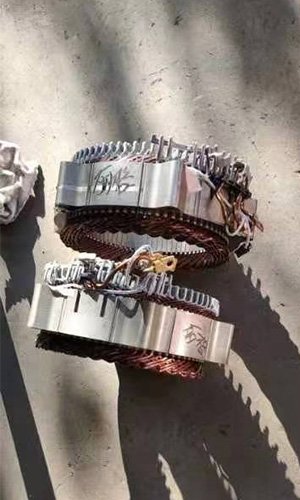
Stator Core:
It is an important part of the motor, on which the stator winding is placed. It is a hollow cylinder made of silicon steel sheets with an insulating layer on the surface, and there are evenly distributed slots inside the core to embed the stator winding. This design helps to reduce eddy currents and reduce energy losses.
Stator Winding:
A component of the motor circuit, consisting of copper wires wound on the stator slots. The introduction of alternating current can generate a rotating magnetic field. These windings are embedded in each slot of the stator according to a certain pattern. The stator winding materials are mainly copper and aluminum. Usually, we call the motor with stator winding composed of copper wire a copper motor, and the motor with stator winding composed of aluminum wire an aluminum motor.
2. Motor Rotor
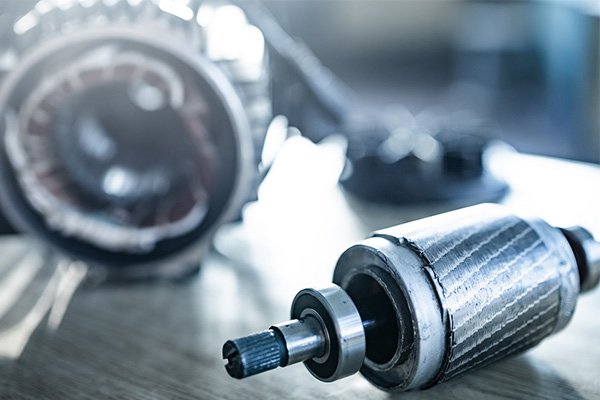
The rotor is the central component of the motor fixed to the shaft. The most commonly used rotor type in AC motors is the squirrel cage rotor. The squirrel cage rotor is cylindrical and is also made of stacked silicon steel sheets. The conductor bars are die-cast into slots evenly distributed around the cylinder. After the conductor bars are die-cast, they are electrically and mechanically connected to the end rings. The conductor bars of pure copper motors are cast from copper, while the conductor bars of aluminum motors are made from aluminum.
3. Motor Casing
The motor casing is a protective device for the motor, protecting the internal components from dust and other contaminants. It is made of silicon steel sheets and other materials using stamping and deep drawing processes. In addition, surface anti-rust and spraying processes can well protect the internal equipment of the motor.
Ⅳ. Pure Copper Motor VS Al Motor
Pure copper motors and aluminum motors each have different characteristics and advantages, suitable for different applications. As a leading scrap metal recycling machine manufacturer, in this article, we will explore the differences between pure copper motors and aluminum motors to help you quickly determine which motor is more suitable for scrap metal recycling machines.
1. Source of materials
As a limited resource, the number of known copper mines is indeed small, and copper mostly exists in compounds in nature, requiring complex electrolytic refining to obtain clean pure copper for mechanical manufacturing. Aluminum is a cheaper and more common alternative metal. The global basic bauxite resource reserves are 31.3 billion tons, which is 50 times the reserves of copper mines. Moreover, the chemical properties of aluminum are more active, and it is easier to obtain pure aluminum. Therefore, using aluminum to make motor windings is a more common choice.
Summary: Due to the abundance of aluminum ore resources, using pure aluminum to make motor windings is a more common choice; copper resources are scarce, and extracting pure copper from copper mines is time-consuming and labor-intensive.
2. Manufacturing Process
Pure copper has high mechanical strength, so it is easier to wind the stator with copper. However, pure aluminum has low toughness and is easy to break when winding the stator, which affects the motor’s qualification rate.
Secondly, the density of copper is 8.960g/cm³, while aluminum is only 2.7 g/cm³. If you want to get the same motor power, you either need to use aluminum wire with a larger diameter or make the number of turns of aluminum wire greater than that of copper wire. This involves issues of stator slot opening and winding filling. Using aluminum windings for winding requires replacing a larger stator core, which will increase the size and weight of the motor and affect the design and appearance of the metal recycling machine.
Summary: The manufacturing process of copper motors is relatively simple, and they are more compact than aluminum motors, making them ideal for compact mechanical designs.
3. Conductivity
The conductivity of copper wire is better than that of aluminum wire. The current carrying capacity of copper wire is 6A per meter, while that of aluminum wire is 5A, so the current passing through copper wire per unit time is better than that of aluminum wire. This provides a steadier and more efficient current supply to the pure copper motor, improving processing efficiency and reliability in scrap metal recycling machine applications.
Summary: Pure copper motors provide efficient and stable current conduction, ensuring higher performance in scrap metal recycling applications.
4. Energy Saving
Copper has a lower electrical resistance than aluminum, which means that when current flows through the copper winding, less energy is lost as heat. And because copper generates less heat under the same current load, the current is smooth, which can effectively reduce the loss during power transmission. If aluminum wire of the same wire diameter is used instead of copper wire, the motor loss will increase by at least 3%.
Summary: Pure copper motors have lower heat generation, lower loss, and are more energy-saving. In applications such as scrap metal recycling that require long-term continuous operation, more energy-efficient copper motors can help recyclers reduce operating costs.
5. Working Life
Pure copper motors have low losses and low heat generation, so the operating temperature of the rotor and stator in the motor is lower. This means that the motor can work for a longer time without causing damage to components, ensuring the reliability and stability of the scrap metal recycling machine. Aluminum motors generate more heat and are easy to burn out, so they are suitable for scenes with short intermittent working time.
Secondly, pure copper materials not only have better corrosion resistance, but also higher mechanical strength and fatigue resistance. Under long-term working conditions of more than 6 hours, the internal mechanical parts of pure copper motors can withstand greater impact forces and reduce wear caused by material fatigue or corrosion.
Summary: Pure copper motors are more durable than aluminum motors
6. Noise Impact
For every 3 decibel increase in noise, its energy will double. Aluminum wire motors generate more heat, so the need for fan cooling is greater. The noise it generates is about 7 decibels higher than that of copper wire motors, and the energy it generates is twice that of pure copper motors. Workers who are in a high-noise environment for a long time may suffer from a variety of health problems such as high blood pressure, tinnitus, and hearing impairment.
Summary: Pure copper motors have less noise impact and create a healthier working environment
7. Security Issue
First, copper has a higher melting point and better heat resistance than aluminum, reducing the risk of insulation breakdown and fire, and making copper motors more robust under continuous high-load operation. Second, copper is more chemically stable than aluminum and is less susceptible to oxidation. Aluminum easily oxidizes at connection points and can lead to overheating, poor conductivity, and even wire breakage. Finally, copper has higher mechanical strength, making it more resistant to wear, bending, and breaking, while physical shock or vibration may compromise the safety of aluminum-wound motors.
Summary: Copper has a higher melting point, better heat resistance, and stronger chemical stability and mechanical strength, which makes scrap metal recycling machines using pure copper motors safer and more reliable.
8. Cost
Copper is much heavier than aluminum and more expensive. Even if an aluminum motor needs a larger diameter core and more windings to achieve the working effect of a pure copper motor, the price of the copper winding itself has completely exceeded these additional materials. Considering economic factors, aluminum motors are much cheaper than pure copper motors.
Summary: Aluminum motors have a much lower economic cost than copper motors, making them suitable for limited budgets.
9. Post-Maintenance
The melting point of copper is 1083.4℃, and the melting point of aluminum is 660℃, which is much lower than copper. However, aluminum motors are very difficult to repair because they cannot be welded. This is because aluminum is very active in chemical properties and easily forms a dense oxide film when in contact with air. Its melting point is 2050℃, which causes the aluminum winding to be unable to melt and fuse normally during welding maintenance. Copper has strong plasticity, so copper motors are relatively easy to repair.
Summary: Copper motors are relatively easier to repair, while aluminum motors require more complex welding processes because of the oxide film.
In general, pure copper motors have obvious advantages in performance, durability, efficiency, etc., including better conductivity, lower noise, longer service life, higher safety, etc. Although aluminum motors are a more economical choice, they are not suitable for the long-term operation of scrap metal recycling machines due to their lower conductivity, shorter service life, higher noise, and safety risks. Therefore, we believe that copper motors have excellent reliability and efficiency, making them the best choice for professional metal recycling machinery.
Ⅴ. Applications of Pure Copper Motors
1. Home appliance field
Pure copper motors are widely used in home appliances such as washing machines, vacuum cleaners, and soybean milk machines because they offer great advantages in terms of service life and efficiency.
2. Automobile field
In the automobile field, pure copper motors are mainly used in high-load fields such as automobile engines. Since pure copper motors have better conductivity and higher efficiency, they can better meet the high power requirements of automobile engines.
3. Mechanical field
Pure copper motors are very suitable for use in high-speed rotating equipment. Since pure copper motors have high efficiency and long service life, they can meet the needs of mechanical equipment under high loads and high-speed rotation.
All scrap metal recycling machines manufactured by our company, including cable shredding machines, wire stripping machines, radiator recycling machines, electric motor recycling machines, and a series of other large and small machines, are all use pure copper motors. This ensures that our machines can maintain strong power when working, making high-speed rotating blades easily cut scrap metal materials. At the same time, under the same power, our scrap metal recycling machine has better heat control, reduces power consumption, and is more energy-saving. Although the cost is slightly higher than that of the scrap metal recycling machine with an aluminum motor, our pure copper motor scrap metal recycling machines have a long service life and do not need to spend a lot of cost and energy on maintenance.
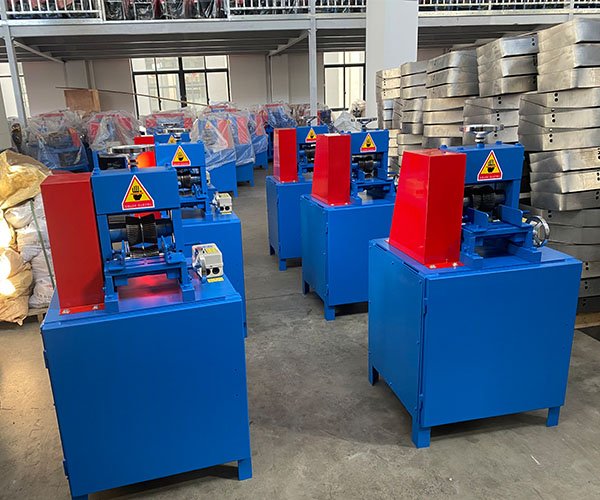
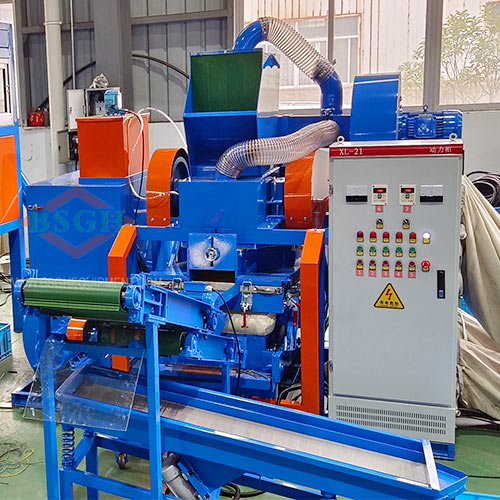
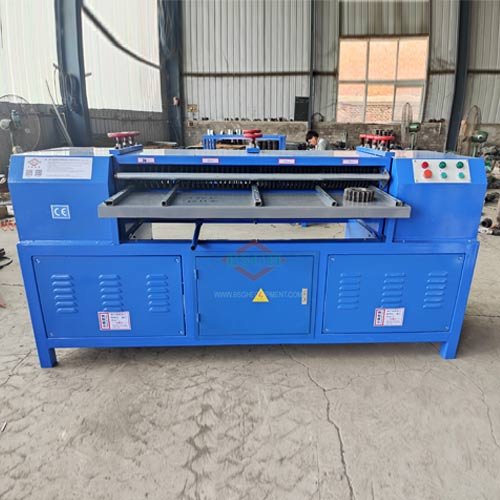
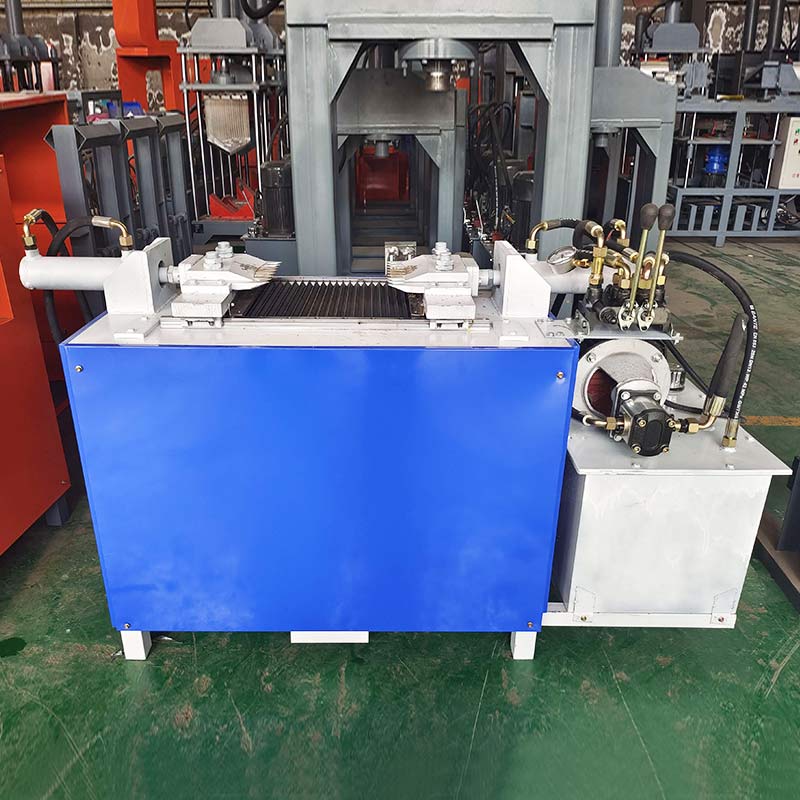
Ⅵ. Conclusion
There are many benefits to using pure copper motors.
- First of all, its electrical conductivity is very good, which can transmit electrical energy more efficiently, making the operation of the scrap metal recycling machine more stable and reliable.
- At the same time, the thermal conductivity of pure copper core motors is also very high, which can dissipate heat better in high-temperature environments and extend the service life of the recycling machine.
- In addition, aluminum motors require more additives and chemicals in the manufacturing process, which causes certain environmental pollution. The manufacturing process of pure copper core motors is relatively simple, and the materials used are more environmentally friendly.
Therefore, in the field of industrial recycling, since you will use the machine for a long time and at a high frequency, BSGH Granulator scrap metal recycling machines all use pure copper motors. Considering pure copper core motors have strong conductivity, less heat during operation, and relatively long life, our scrap metal recycling machine can meet the needs of high load, long time, and high frequency of use, ensuring safe and reliable operation after adopting pure copper motors.
About US
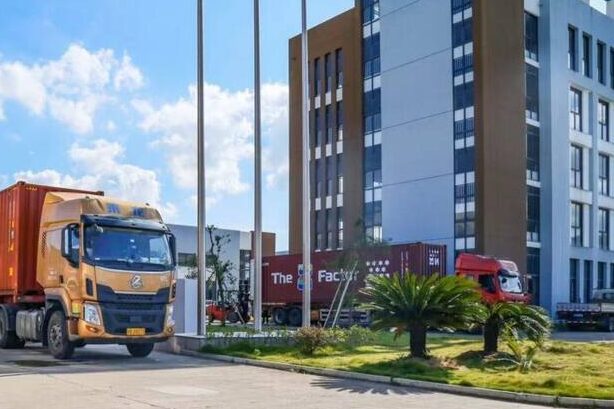
BSGH Granulator has been focusing on the field of scrap metal recycling for more than 25 years. We are one of the earliest high-end brands of copper rice machines in China. We can provide you with mature manufacturing processes and advanced double separation technology to achieve a 99.9% copper rice separation rate so that you can obtain higher quality clean copper particles. We assure you that all our machines use high-quality national standard pure copper motors to ensure that our machines can work longer, have stronger recycling efficiency and create greater value for you.
If you have any questions, please contact us at 0086 13772508206.